Customers Feedback
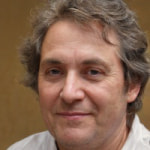
The craftsmanship is stunning Read More
I’m absolutely thrilled with the bronze Lady Justice statue I purchased! The craftsmanship is stunning, with incredible attention to detail. It’s even more beautiful in person than in the pictures. The material feels solid and high-quality, and it’s clear a lot of care went into making this piece. It’s now the centerpiece of my collection, and I couldn’t be happier. Highly recommend to anyone looking for a unique, meaningful sculpture!
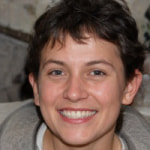
Excellent service and communication Read More
Excellent service and communication. Jane stayed with from placing the order until delivered to my house .you are a star Jane stronley recommended thanks
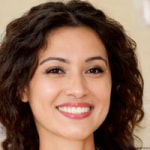
The craftsmanship is impeccable Read More
I recently purchased a marble washbasin from YOUFINE, and I am extremely impressed with both the product and the service! The craftsmanship is impeccable, with a smooth, polished finish that gives my bathroom a luxurious and sophisticated feel. The quality of the marble is outstanding, and it’s clear that YOUFINE takes great pride in their work. The customer service team was very helpful, ensuring a seamless experience from order to delivery. The washbasin was well-packaged and arrived in perfect condition.
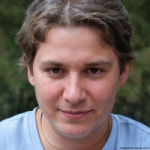
Extremely satisfied with my purchase Read More
I am extremely satisfied with my purchase from Youfine Art Sculpture! The service was excellent, with friendly and helpful staff. The shipping was fast, and the quality of the sculpture is outstanding. The polishing is incredibly shiny, and the welds are meticulously smoothed. The craftsmanship is truly impressive. I will definitely recommend this store to my friends!
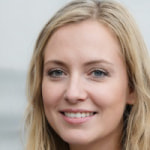
Customer service was very good Read More
Words just aren’t enough. I love the finished product. The Sled is Beautiful and I can’t wait to display it in my yard this Christmas. The communication was amazing and the overall customer service was very good!!! I am already planning another order for this next year. I WILL ONLY DO BUSINESS WITH THESE GUYS!!!!!
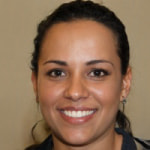
High quality sculpture Read More
Very nice, high quality sculpture. I love my sculpture. The supplier delivered as promised. They always replied my questions on time and patiently. Finally, the statue arrived smoothly under their help. I appreciate it very much.
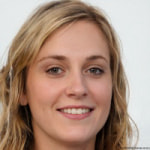
Such beautiful workmanship Read More
I researched many of the statues and decided to order the four marble statues from this company. I worked with Caroline who was very professional and kind. Whenever I had a question she was quick to answer. My statues arrived and they were delivered to the location I wanted. They were packed in crates and wrapped up tight and secure. When we opened them up they were even better in person than in the photos. Such beautiful workmanship! I just love them!
Previous
Next